THE AEROSOL JET TECHNOLOGY
Printed electronics has been emerging as promising candidate in fields such as diagnostics or tissue engineering, with technological platforms giving feedbacks on biological samples or physiological processes, considering the recent attention for disposable and/or low-cost and reliable interface systems. Among printing methodologies, aerosol jet printing is an additive process that permits to deposit a wide variety of materials (conductive inks, dielectrics, nanotubes, epoxies, polymers, biological materials and more) on many substrates (e.g., metal, plastics, glass, paper, silicone) without expensive masks, instruments for thick-film deposition, or post-patterning techniques. This process consists of four key steps, i.e., atomization of the ink, densification of the generated aerosol, focusing of the aerosol, and deposition of the droplets on the substrate. First, the aerosol is generated, by using an ultrasonic or a pneumatic atomizer, according to the viscosity characterizing the ink to atomize. After generation step, aerosol is focused through a deposition head, in a way to form a continuous beam of liquid droplets, which is kept coaxial with an annular inert gas (usually nitrogen). This gas prevents the aerosol from being in contact directly with printer nozzle. Then, the aerosol can be deposited on both planar and even non-planar complex surfaces, thanks to its focusing system. The University of Brescia has a very advanced system, i.e., Aerosol Jet Printer AJ 300-UP from Optomec Inc., which permits to reach high deposition performances. For instance, printed track can have a width up to 10 um, whereas layer thickness can be as small as 100 nm.
a
THE PHOTONIC SINTERING
After deposition, printed object may require further treatments, for example sintering, which may result fundamental for its final characteristics. Among sintering techniques, photonic sintering is an innovative methodology that heats a sample with pulsed light. The heating process is accomplished thanks to a couple of xenon flash lamps, which radiate energy, focused by mirrors, toward the sample. Anyway, the greatest part of sample substrate remains relatively cold, since light exposure is in the order of milliseconds (thus reducing processing time). This produces minimal damage on substrate material and avoids unwanted processes (e.g., diffusion), permitting to work with cheap and flexible substrates with low-flame temperatures, such as plastics and paper, which could not be employed so far. Photonic sintering is carried out at the University of Brescia, thanks to the PulseForge® 1300 system, by Novacentrix, which first developed the technology.a
a
a
EXAMPLES OF REALIZED OBJECTS
-
force sensors
-
temperature sensors
-
strain sensors on metal and plastic substrates
-
chemical sensors
-
electronic circuits, connections, pads, antennas both on 2D and 3D surfaces
-
surface finishes either conductive or insulating
-
circuits and sensors on paper and fabrics
-
microchannels and microstructures for microfluidics
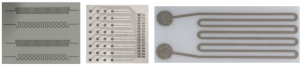
From left to right: connections for surface electromyography (EMG) sensors printed on polyurethane substrate; surface EMG electrodes and their connections printed on cotton substrate; stretch sensor for the monitoring of human joints movement printed on a stretchable substrate.
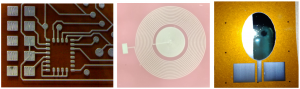
From left to right: connections printed on a planar flexible surface; antenna printed on silicone substrate; superficial finish printed on flexible kapton substrate.
a
DEMO VIDEOS
A
A
A
A
A
A
ARTICLES FROM LOCAL NEWSPAPER “GIORNALE DI BRESCIA”
A
For more info on both aerosol jet printing and photonic curing, please contact Mauro Serpelloni or Edoardo Cantù, or visit the official website.